Technology & Design
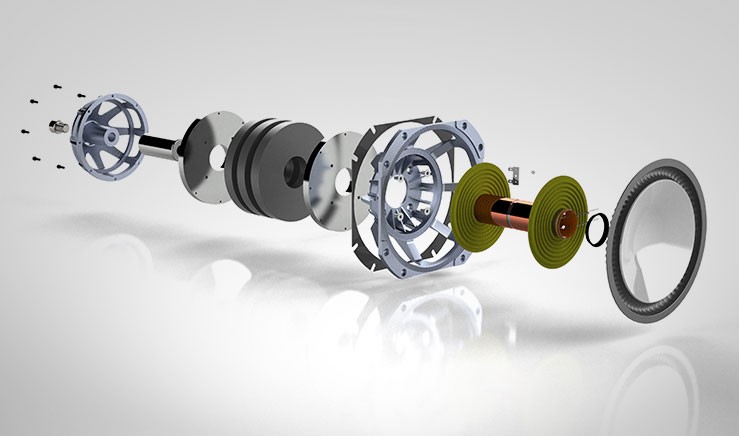
Science of Sound
Paradigm harnesses technology in the service of sound.
Read More keyboard_arrow_right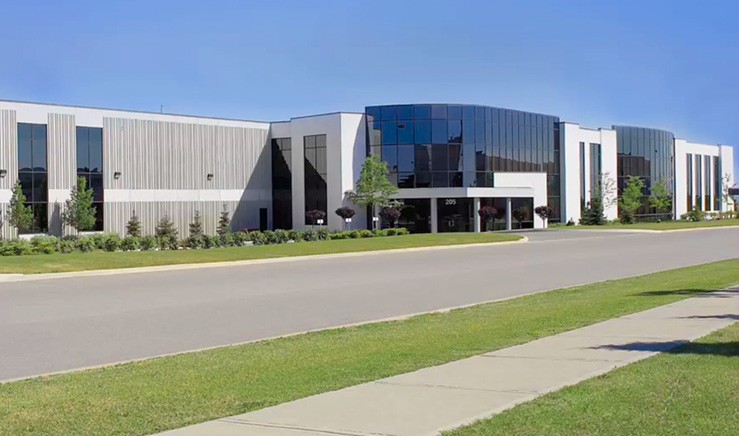
225,000 square feet of amazing
Welcome to North America's most advanced loudspeaker factory.
Read More keyboard_arrow_right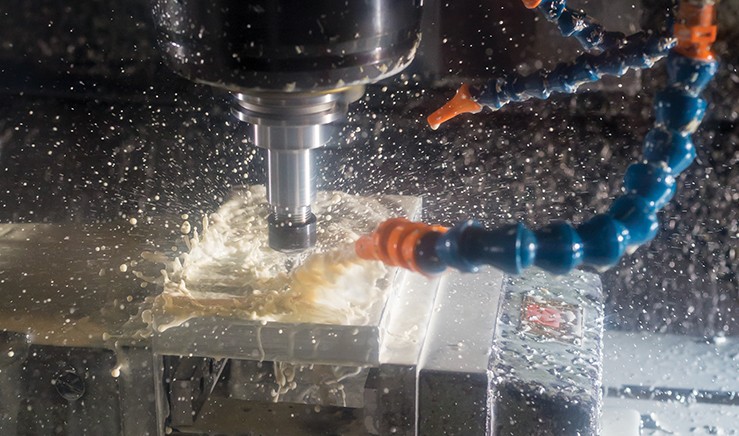
We're a little obsessed about measuring things
Exact measurements & critical testing achieve The Paradigm Sound.
Read More keyboard_arrow_right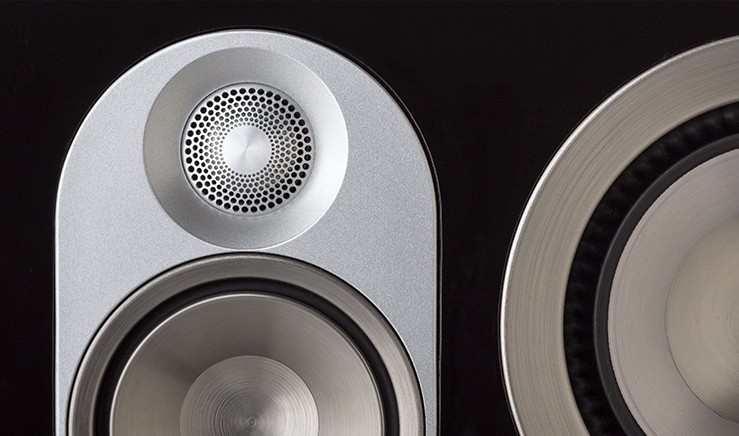
Loudspeaker Components Explained
All the ingredients you need for high performance audio.
Read More keyboard_arrow_right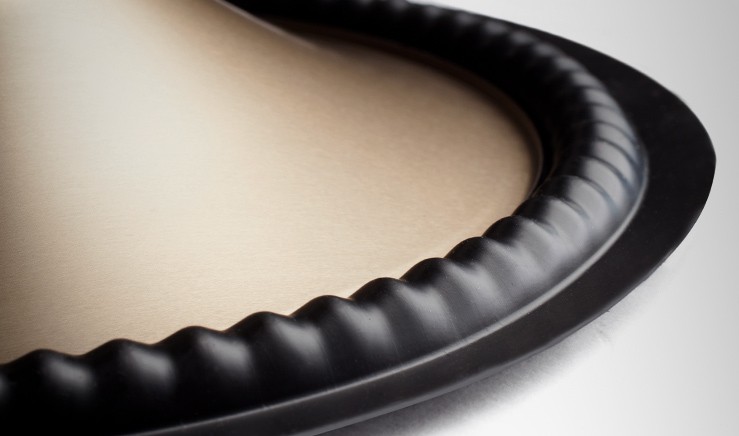
Patented Active Ridge Technology (ART™) Surrounds
More durable, more reliable, for a long life of high performance.
Read More keyboard_arrow_right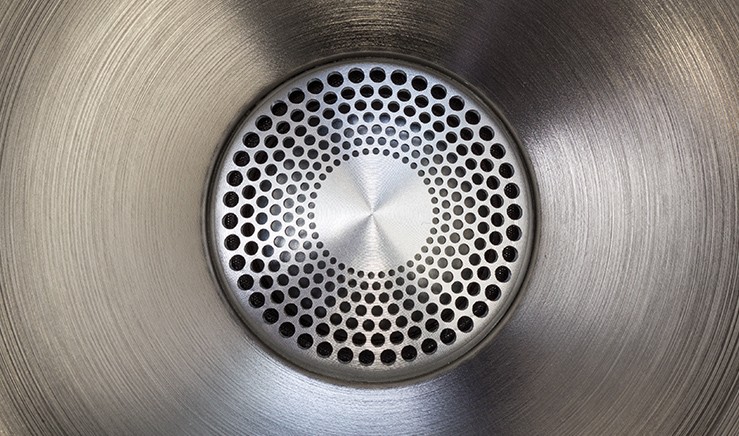
Patented Perforated Phase-Aligning (PPA™) Lens
A new take on the phase plug, the PPA smooths output without coloring the sound.
Read More keyboard_arrow_right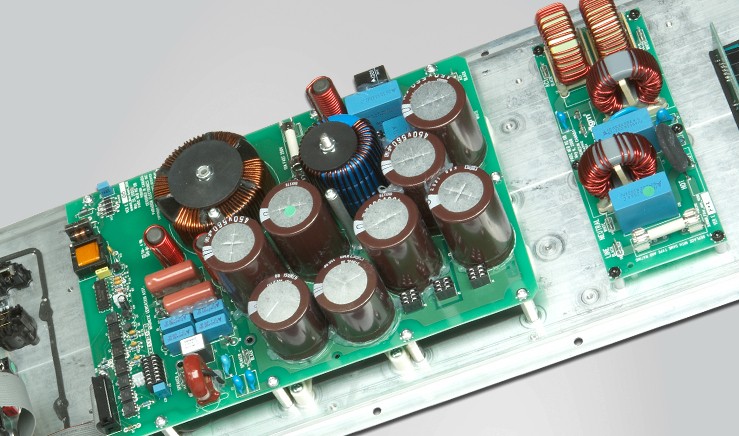
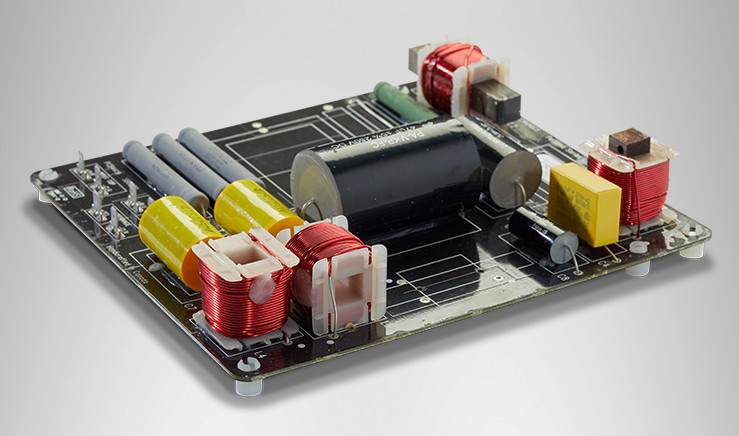
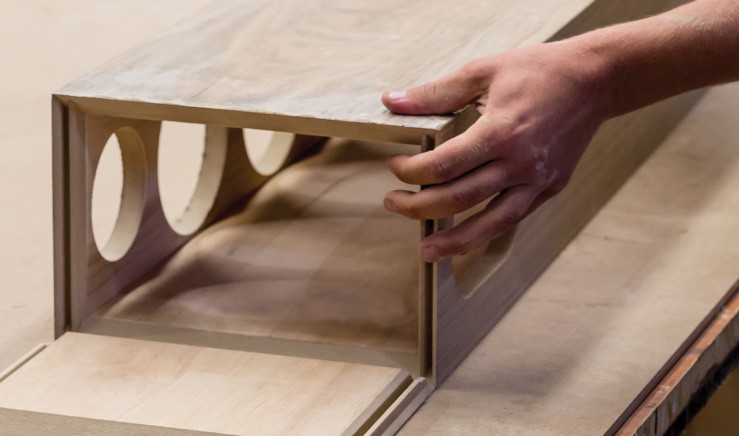
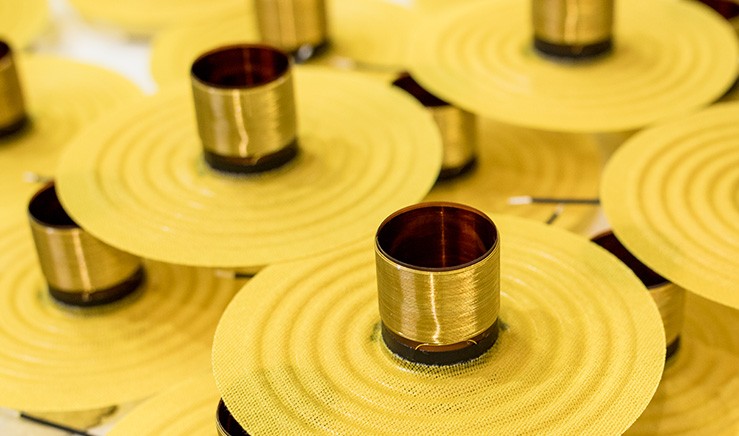
Quality is more than a buzzword
Listen: our dedication to quality is obvious.
Read More keyboard_arrow_right